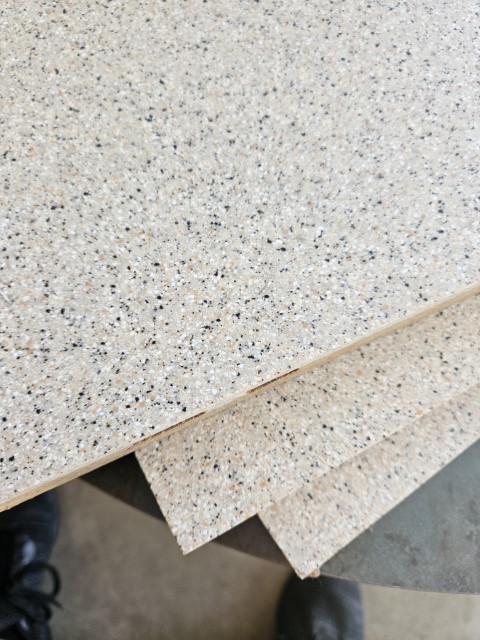
The first project of the year is another that I never got around to working on. These are 1″ thick panels made from 1/4″ thick solid surface material glued to 3/4″ thick particle board. I acquired them several years ago while working at a cabinet shop.
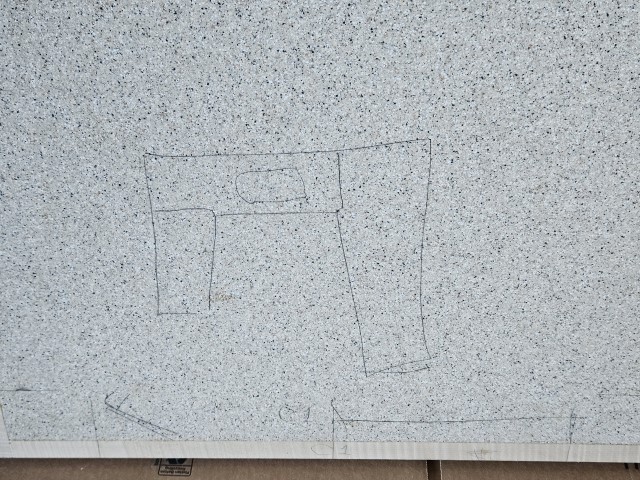
These panels are what the solid surface manufacturer used to train us how to use their product to make countertops. After the training session, the representative asked if anybody wanted them. Nobody else saw their potential, so I happily claimed them for myself.
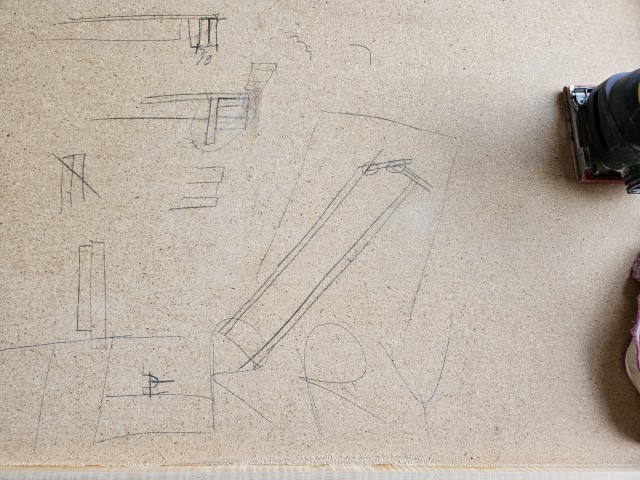
I didn’t know what else I was going to use to complete the project, but I knew what I’d be most likely to use. Having no equipment at home, I used the panel saw at work to cut them to size for what I had in mind.
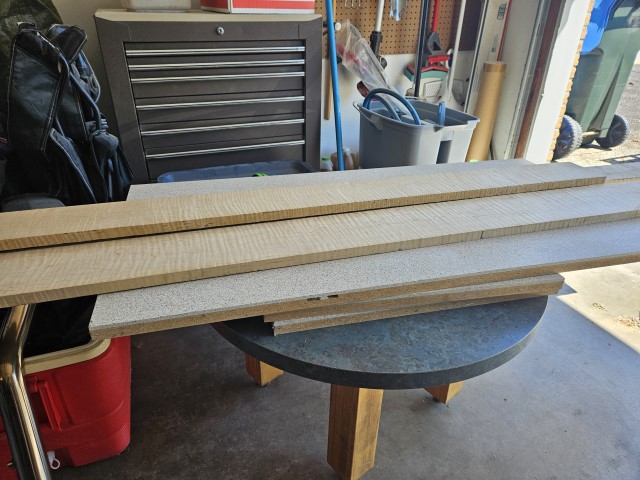
I already had a few nice maple boards I bought from one of my previous employers. They were just the right size for this project, and there would be very little waste. Dad and I went over my plan and mapped out how and where each board would be used.
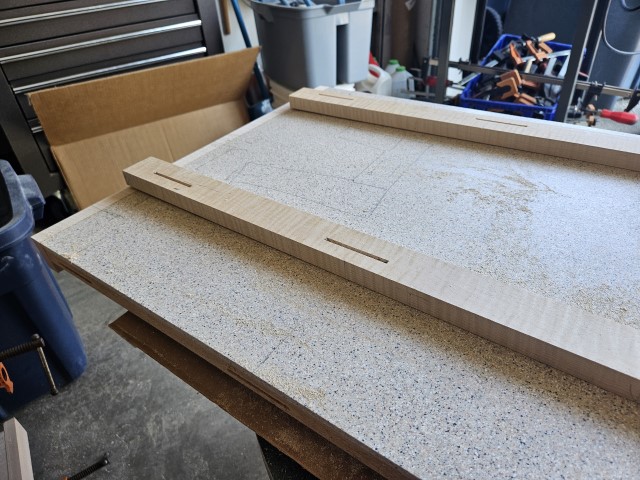
Dad took them home and ripped them to width on his tablesaw. Back in my garage, he measured and cut the end boards to length and cut slots for the biscuit joints. Then he applied glue to the board and the biscuits and applied clamps.
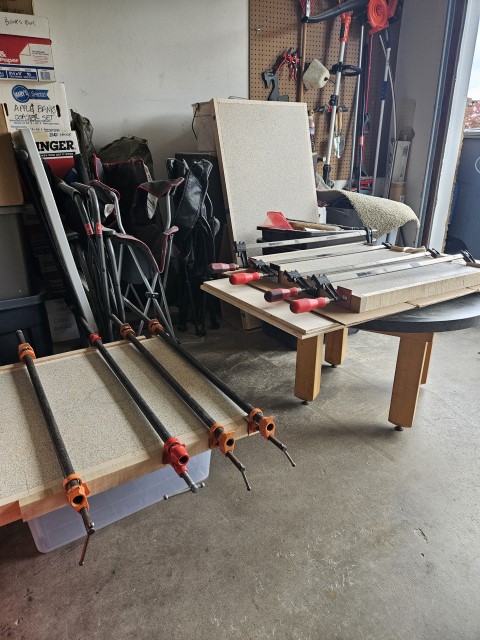
We took a break while we waited for the glue to dry. Then Dad measured and cut the boards for the other sides and repeated the gluing process.

This board had a damaged edge that prevented us from attaching it in the desired orientation. So we flipped it end for end to put the damage where the router would take care of it. That’s why the ‘witness marks’ don’t match (see below).
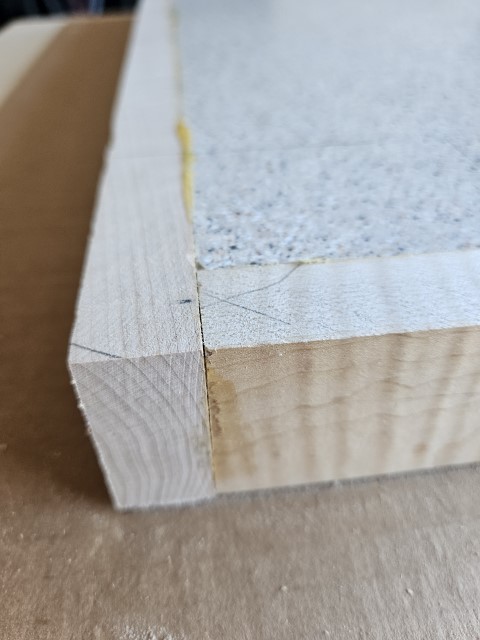
We called it a day and Dad went home. It was then up to me to wait for the glue to dry, sand the joints flush, sand out the saw marks, and flatten the rippled surface caused by the woodgrain.
Exciting! I love your project blogs, although I still need to catch up on the desk—thanks for this reminder! I’m curious if a “hairpin table” describes its shape or has another definition, what size and intended usage will they be, and how soft/stable is the soft material (can you balance a glass on it and would you want to)? Guess I’ll find out these and answers in future installments!
The figure on the maple boards is *fire*! Perhaps, dare I even say, *flame*!